What a Cup of Coffee Can Teach Us About AI-Driven Manufacturing
I believe we are at a pivotal moment in technological advancement poised to revolutionize industrial operations. The convergence of modern generative AI (genAI) and multi-agent capabilities with the past decade of data harmonization and several decades of increasingly more sophisticated process control systems has created a powerful foundation for autonomous factories. I see these technology cornerstones integrating, enabling factories to not only monitor and analyze operations but also to anticipate deviations, simulate corrective actions, and autonomously execute decisions.
But first, let’s talk about coffee.

The Coffee Cup Story
Have you ever reached for a cup of coffee only to find it empty? That momentary jolt of frustration is a “prediction error,” where your brain’s expectation didn’t match reality. Your mind quickly reevaluates the situation and drives you to act — whether to search for the coffee pot or wait until after the meeting. This need to close the gap between expectation (a full cup) and reality (an empty cup) is a core principle of prediction error minimization.
Your brain doesn’t stop at noticing discrepancies; it actively seeks to resolve them by weighing options in context, simulating scenarios, and choosing the best action to minimize the gap. A vast majority of such decisions are made subconsciously, as your brain handles routine scenarios automatically. Your conscious attention only gets involved when the trade-off is complex or stakes are higher, requiring more deliberate thought. This constant cycle of prediction and correction — deciding whether to refill now or wait until after the meeting — not only illustrates human adaptability but may also serve as a blueprint for the AI-driven systems that can transform industrial operations.
I believe we are swiftly reaching a point of technological maturity where we can emulate human-like capabilities within industrial operations. This belief is driven by the ongoing transition from ‘big data’ to ‘big compute’, fueled by recent breakthroughs in generative AI (genAI) and the emergence of modern multi-agent workflows. Together, these technologies can provide AI systems with intuitive natural language interfaces, sophisticated reasoning and decision-making abilities, enabling seamless collaboration and more intelligent, autonomous industrial processes.
By building AI systems that can anticipate deviations, simulate corrective actions, and autonomously decide when to escalate issues, we can start to transform industrial operations.
A systematic approach
One approach to building the autonomous factory is to develop four AI systems that co-evolve and work in harmony. Each system seeks to fulfill a distinct objective: Assist, Self-Monitor, Strategize, Act. There are technical overlaps and synergies between these systems. But they will each have a distinct end-user proposition which is crucial in order for proper training to take place.
System 1: The virtual industrial assistant — your next employee
The first step toward an autonomous factory is enabling seamless communication between you and the factory itself. This involves teaching AI agents to collect, analyze, and synthesize operational data from all sources within the factory’s physical environment and internal context. The outcome is a virtual assistant designed to function like an invaluable team member.
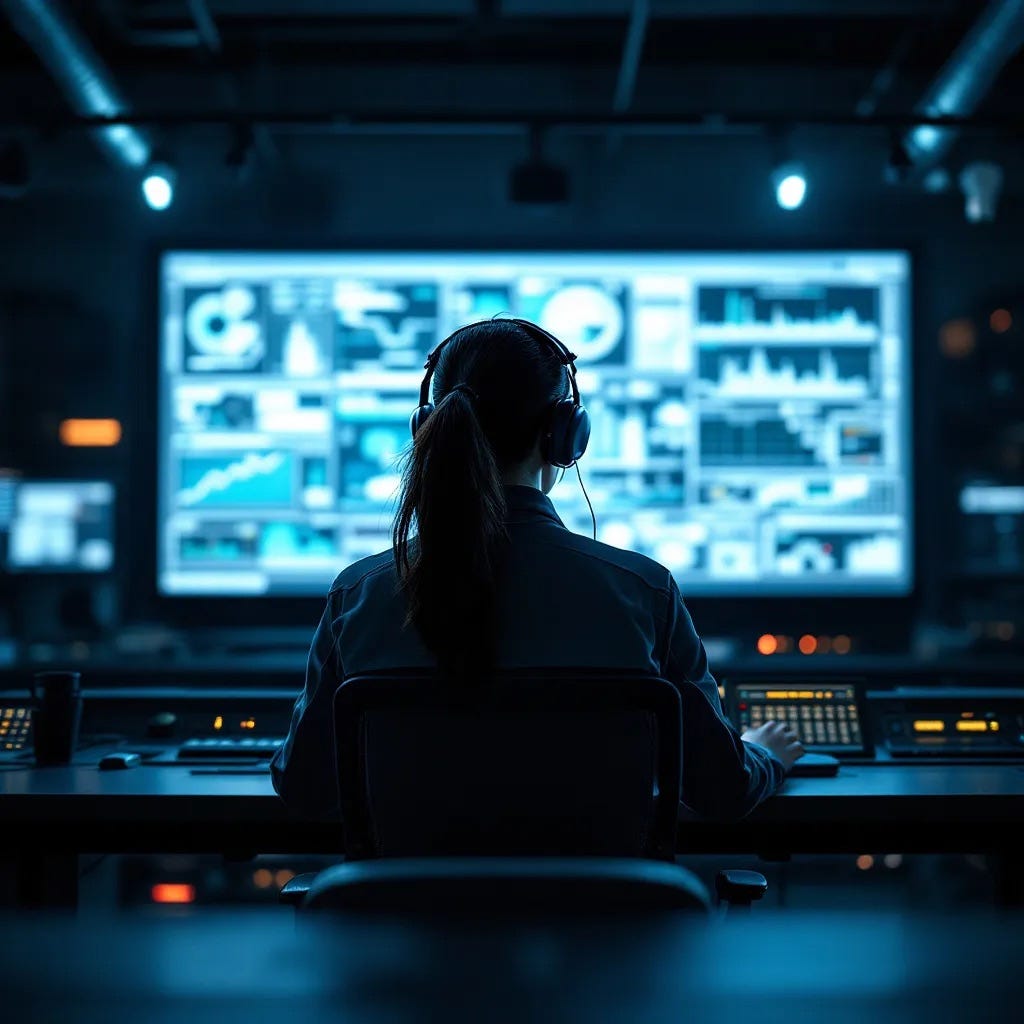
Imagine asking questions like, “What’s behind the increased energy consumption in block 3?” or “How has furnace performance trended over the past month?” The AI responds as if you were consulting a team of engineers, delivering precise and contextual answers in well-structured text and helpful visualizations. You can request deeper analyses, ask follow-up questions, and even set up automatic monitoring for specific issues — much like delegating tasks to a human assistant.
To build this system, three technical capabilities are essential:
- Robust data integration foundation: A secure, scalable integration layer that standardizes access to diverse industrial information and data lakes. This includes sensor data, process performance metrics, maintenance and asset documentation, standard operating procedures, and more.
- Comprehensive domain representation: A detailed digital model that accurately captures the physical reality and relationships between components, equipment, assets, instrumentation, and data sources.
- Reliable computation orchestration engine: A transparent system that executes algorithms and models reliably, either on demand or on schedule, with full contextual awareness of the underlying domain and available data.
With these prerequisites in place, we can create intuitive natural language interfaces that interact with task-specific AI agents for reasoning, data collection, code execution, data visualization, and insight synthesis.
Through these interfaces, operational managers can get a comprehensive, real-time understanding of plant operations without relying on rigid dashboards, hard coded workflows or manually generated reports. The virtual assistant acts as a team of specialized engineers, dynamically gathering, contextualizing, and analyzing data. This empowers operators and engineers to ask any question through text or voice and receive precise, contextual answers — enhancing visibility into plant performance and enabling more informed decision-making.
While System 1 offers significant value it remains inherently reactive and requires prompting. You can automate your favorite prompts, much like daily procedures for your team, but you will only obtain the insights you actively seek. System 1 responds to the questions you ask, whereas System 2 takes it further by continuously monitoring and learning without needing to be prompted.
System 2: The factory’s virtual limbic system — Self-Monitoring and Learning
To achieve an autonomous factory, we need a self-monitoring system that continuously processes information, detects deviations, and updates its understanding of the factory’s various operational states. This mirrors the brain’s approach to prediction error minimization — constantly comparing expected outcomes with actual results to refine its models. Just as a human engineer adjusts their understanding of a plant’s behavior over time, the system updates its internal models, minimizes prediction errors and becomes increasingly accurate and responsive. This evolution from prompt-induced diagnostics to self-awareness sets the stage for something even more impressive: a factory that truly knows itself.
It takes a human being 15–18 months to develop a basic sense of “self,” e.g., enabling them to recognize themselves in a mirror. Industrial operations have a distinct advantage over human infants: historical data. Once we establish a robust system for monitoring and learning, we can process years of historical data through this system to accelerate the learning process. Much like humans, the more deviations and problems present in the data, the more the system learns about itself. Additionally, it requires external input — akin to guidance from “grown-ups” — to accurately label which states are productive and which are not.
With System 2 in place, managers gain a powerful tool that automatically identifies potential issues and learns continuously. This allows Subject Matter Expert (SME) teams to focus on higher-level problem-solving rather than tracking deviations and chasing alarms. The system provides operators and plant managers with a continuously improving source of insight that highlights patterns before they escalate into significant problems.
While System 2 offers tremendous value by laying the foundation for self-monitoring and continuous learning, I believe we’re only scratching the surface of what’s possible. Even a self-aware plant lacks the capability to navigate the intricate trade-offs between equally safe internal states and conflicting cost-benefit business objectives. This is where System 3 comes into play, introducing additional layers of prediction error minimization to make sophisticated, informed decisions.
System 3: The Factory’s Virtual Prefrontal Cortex — Advanced Reasoning and Strategic Recommendations
Ever been to CBT (cognitive behavioral therapy)? Here’s an exercise you can try when faced with difficult choices: assign each option to a side of a die or a coin, roll it a few times, and pay close attention to how each outcome affects your internal state. This simple activity mirrors how your brain makes decisions by running simulations, evaluating each outcome against your hierarchy of goals (your internal value system), and thereby minimizing prediction errors to achieve desired states.
System 3 elevates the concept of prediction error minimization by introducing sophisticated computational layers that emulate the complex decision-making processes of the human brain. Just as our brains continuously refine decisions based on feedback and evolving goals, System 3 not only predicts outcomes but also assesses the accuracy of these predictions against real-world results. This multi-layered approach ensures that the system not only plans actions to achieve objectives but also learns from the discrepancies between expected and actual outcomes to enhance future predictions. Think of it as the inner dialogue that resolves conflicting priorities, ensuring decisions are aligned with overarching goals.
We need a system that embodies this prediction error minimization process. It should start by taking business goals as inputs — such as increasing throughput, reducing costs, capping emissions, and complying with safety protocols. The system will then map these goals against valid internal factory states and run simulations of potential operational actions to achieve the desired outcomes. By predicting the outcomes of various actions and comparing them against desired goals, the system tries to find the optimal trade-off, ensuring that the factory’s operations align closely with strategic objectives. Think of System 3 as the factory’s prefrontal cortex — the part of the brain responsible for complex cognitive behavior, decision-making, and moderating social behavior.
As this system deepens its understanding, it will analyze data and autonomously propose optimizations, creating a step-change in how teams prioritize and implement improvements. Operators can then validate these recommendations, building trust and confidence in the system’s ability to guide operations.
A system like this promises tremendous value and brings us closer to our vision of a sentient and autonomous factory. However, we are still reliant on the grace of busy humans to implement these recommendations. Now, with System 3 providing you with expert recommendations, System 4 takes us into the future where factories can act on those recommendations autonomously.
System 4: Autonomous Operations and Action Execution
Needless to say, automation is nothing new to industrial operations. Process control systems like SCADA (Supervisory Control and Data Acquisition) and PLCs (Programmable Logic Controllers) have been the backbone of automation for decades. While these systems have been instrumental in automating routine tasks, maintaining consistent production flows, and ensuring operational stability across various manufacturing environments, they come with inherent limitations. For instance, they are confined to fixed rules and predefined parameters, operate reactively rather than proactively, and require humans to interpret data and draw out insights. Even more advanced process control systems that offer enhanced analytical capabilities are limited to specific tasks and lack the flexibility to adapt to unexpected changes or optimize processes beyond their initial programming. Moreover, these systems are unable to learn and evolve continuously, meaning they cannot anticipate issues or dynamically adjust to shifting operational conditions.
System 4 will overcome these limitations. By integrating the self-monitoring, reasoning, and strategizing capabilities of System 3 with traditional process control. All we need to do is parse and integrate these recommendations back into our control systems. Right?
Not quite. Before we can fully entrust these recommendations to an autonomous system, there are a few critical capabilities we need to incorporate into System 4. This includes a confidence scoring system that ensures no actions are taken unless the associated recommendation has a range of potential outcomes within acceptable boundaries. Additionally, an escalation mechanism must be in place to involve a human decision-maker when high-risk or complex trade-offs arise. Initially, these boundaries will be set very carefully, but over time, based on human feedback, the scoring system will update its weights, allowing the boundaries to become increasingly relaxed.
The human analogy here is the sudden “jolt” you feel when you reach for the cup of coffee only to find it empty. This reaction is a result of your limbic system (primarily the amygdala and hypothalamus) assigning an emotional response to this unexpected situation to capture your full attention.
Think of System 4 as the factory’s motor cortex — the part of the brain responsible for executing voluntary movements based on decisions made by the prefrontal cortex. Just as the motor cortex translates strategic decisions into physical actions, System 4 takes the refined recommendations from Systems 1 through 3 and autonomously implements them within the factory’s control systems. This ensures that operations are not only planned but also executed seamlessly and efficiently.
This is the pivotal moment we’ve been waiting for — a future where the factory doesn’t just monitor itself but makes decisions in real-time, self-correcting and dynamically aligning with business outcomes. A future where human intervention is reserved for complex, high-level decisions, while the factory handles the repetitive, data-intensive tasks autonomously
That future is now
At Arundo Analytics we have spent almost a decade building and tuning a world class technology foundation and know-how for integrating industrial data, representing complex physical domains digitally, orchestrating computational models, and providing actionable recommendations. With this as our starting point, we started a journey earlier this year to build what I refer to as “System 1” above. Internally we call this the Industrial AI Companion.
Achieving factory autonomy is no longer a distant dream. It’s a journey we are already on. A systematic approach ensures that value is delivered at every step, while the ultimate goal remains in clear focus: a factory that not only *knows* itself but can *run* itself. This transformation doesn’t just make factories smarter — it also augments human workers, significantly boosting their productivity. It will free up human operators to focus on strategic decision-making, creative problem-solving, and innovation.