Pumps contribute significantly to CO2 emissions. Why? What can you do? How can advanced analytics provide insights into pump performance and help combat this?
CO2 emissions are a major concern for many sectors and people in general. The major CO2 emitters are well known: energy production, agriculture, live-stock rearing, industry, and transportation. However, few associate pumps with CO2 emissions. In this article, I’ll explain why pumps are a significant contributor to CO2 emissions. Secondly, we will look at what can realistically be done to reduce this. And lastly, we will review how advanced analytics can provide insights into pump performance and help combat CO2 emissions as well as improve profitability in a realistic manner.
Before we begin, let me reassure you that this isn’t a novel idea. This has been highlighted by the largest pump association in the world: the Hydraulic Institute. This is what they say:
“when pumping systems are optimized for best efficiency, they improve a company’s profitability with lower energy and maintenance costs, longer mean time between repairs, reduced C02 emissions and a more reliable system overall. Energy savings of (...) 40% or more are possible...”
WHY ARE PUMPS A SIGNIFICANT CONTRIBUTOR TO CO2 EMISSIONS?
The worldwide market for pumps is an estimated US$47.6bn. Pumps are used to circulate, lift, transfer or pressurize liquid, and are common in all industries. Most industries such as chemicals, power generation, agriculture, construction, and mining require pumps to operate. Even though this equipment is ubiquitous and has been used for centuries, between 30% to 50% of the energy consumed by pump systems could be saved.
Just to give you an idea, energy wasted by all pumps operating in Europe could equate to two large power stations (of the size of the Dutch plant Eemscentrale) operating 365 days per year, 24 hours a day at full capacity. Pump inefficiency is well documented and derives from many factors.
WE KNOW PUMPS ARE INEFFICIENT, BUT WHAT DOES THIS HAVE TO DO WITH CO2 EMISSIONS?
Looking at the first pie chart, we can see that electricity can be created by a variety of fossil fuel sources, as well as renewable sources. Almost 40% of electricity in the world is created by burning coal. In the second table, you can see the level of CO2 emissions generated by different fuels. Coal is the number one pollutant. Whilst many countries have access to natural gas, coal is still a predominant source of electricity in the world. As a result, it’s clear that the ubiquitous, largely inefficient pumps are an important source of pollution.
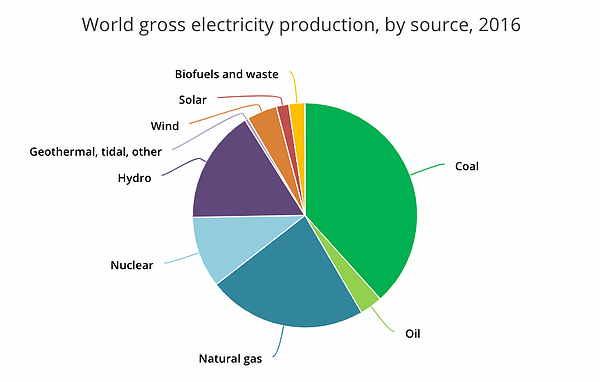
Pounds of CO2 emitted per million British thermal units (Btu) of energy of various fuels:
- Coal (anthracite): 228.6
- Coal (bituminous): 205.7
- Coal (lignite): 215.4
- Coal (subbituminous): 214.3
- Diesel fuel and heating oil: 161.3
- Gasoline (without ethanol): 157.2
- Propane: 139.0
- Natural gas: 117.0
Source: U.S Energy Information Administration
WHAT CAN BE DONE TO SOLVE THIS?
Having seen why pumps can be associated with high CO2 emissions, let’s look at how the industry is addressing this.
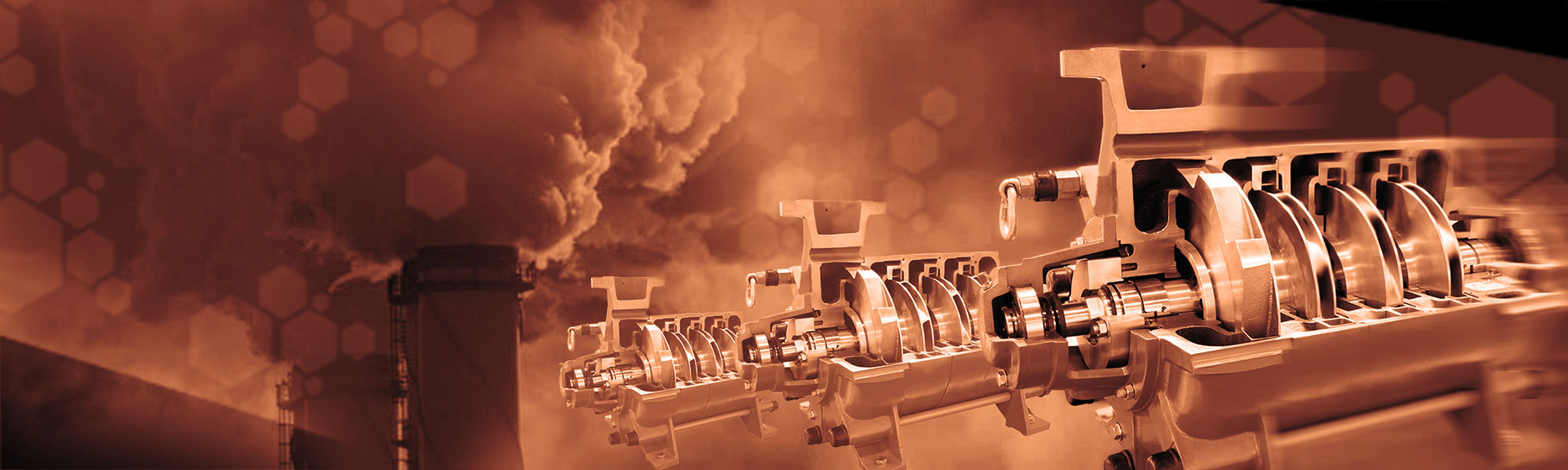
There are many initiatives addressing the energy challenge, such as the ErP (energy-related product) European directive. However, there’s still a high number of old pumps, between 20 to 40 years old running inefficiently and these might not be replaced for decades. From a physical point of view, there are a variety of improvements that can be deployed to address inefficiency, such as:
1. SELECTING THE MOST EFFICIENT PUMP MODEL
When selecting the most efficient pump there are a few factors involved. The type of pump, the size of the impeller as well as the piping size and material which we won’t be discussing here. This will all drive to an improved Best Efficiency Point, the BEP which measures the efficiency of the pump.
2. IDENTIFYING THE SIZE OF THE LOAD USED TO AVOID OVERCAPACITY
Once you have chosen the most efficient model, you should choose the correct capacity. This isn’t a straightforward task. However, it’s a critical one in terms of reducing wasted electricity.
3. RUNNING THE PUMP AT OPTIMAL SPEED
Another important issue is speed. Controlling the speed of the liquid pumped, whether it is high or low speed, is paramount to reduce inefficiencies. According to World Pumps, you can replace throttling valves with speed controls. If the load of liquid pumped is fixed, you need to reduce speed to increase efficiency. If the loads are variable, you could install a parallel system. This requires thorough planning on how the pumps are installed and used.
HARSH TRUTH - IDEAL SCENARIO VS REALITY
Whilst the literature provides many different solutions to this inefficiency, it still remains a challenging task. Many operators have hundreds or thousands of pumps to monitor. Pumps can vary in size and models. Even between two pumps of the same exact model, there will be differences in performance and efficiency. Furthermore, the operators' main priority is to avoid production from stopping at all costs. After that, they’ll focus on reducing maintenance and running costs.
HOW CAN ADVANCED ANALYTICS PROVIDE INSIGHTS INTO PUMP PERFORMANCE AND HELP COMBAT CO2 EMISSIONS?
Advanced analytics for pumps is a powerful tool for increased efficiency. In order to tackle energy efficiency in a sustainable manner, operators should have tools helping them increase the performance of their pumps overall. This will address production loss, maintenance costs and energy costs. Whilst there is no magic wand, pump performance visibility is crucial. By giving operators and maintenance teams a full view of the fleet of pumps, they’ll be able to quickly identify the most inefficient pump.
Advanced analytics is the solution. Operators already have a plethora of data on their pumps. They have operational data such as power, flow, and pressure. They receive design characteristics curves from the pump manufacturers forecasting the behavior and performance of a pump in changing conditions. By comparing actual operational data to design characteristic curves, we can establish a meaningful baseline. This provides context for an increased understanding of a pump’s performance. Once the most meaningful key performance indicators are selected, operators can track the performance and condition of their pumps and put them into operation.
Below is an example of a pump plot. The blue points represent the pump operating in different modes. The yellow area represents the preferred operating region. As the pump moves away from the yellow shade and moves towards the purple shade at the left, it’s operating outside what is called the allowable operating region. This is something all operators want to avoid as it uses more energy, wears the pump down and ultimately causes failures.
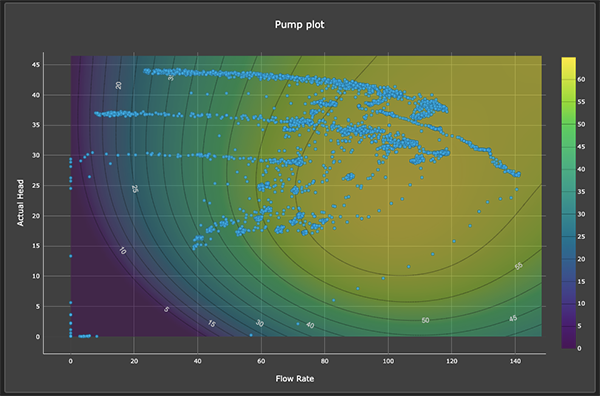
The following chart gives you a glimpse of how this could look for a fleet of pumps. Each bar chart represents a pump. Each color represents an operating region:
- Green: Preferred operating range
- Yellow: Allowable operating range
- Red: Outside of allowable operating range
Instantly you can view which pump requires monitoring.
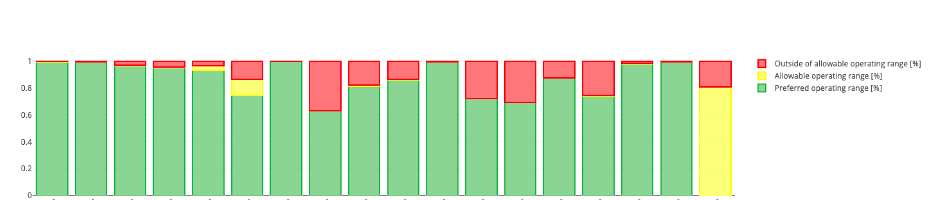

Having a simple way of viewing the worst-performing energy-consuming pumps would be the key to start the journey towards more efficient pumps and a greener world.
CONCLUSION
In the race to reduce CO2 emissions, decreasing the impact of pollution derived by pumps is possible. By improving the efficiency of pumps, not only can you impact the carbon footprint, but maintenance and energy costs can come down too. Through the use of analytics, operators can have complete visibility and ranking of the highest performing and least performing pumps. Once this information is clear, operators can tackle the issue and improve the efficiency of the pump. Awareness of the problem, coupled with regulations, heftier energy bills and more effective tools such as analytics can help drive pump efficiency best practice to the next level.